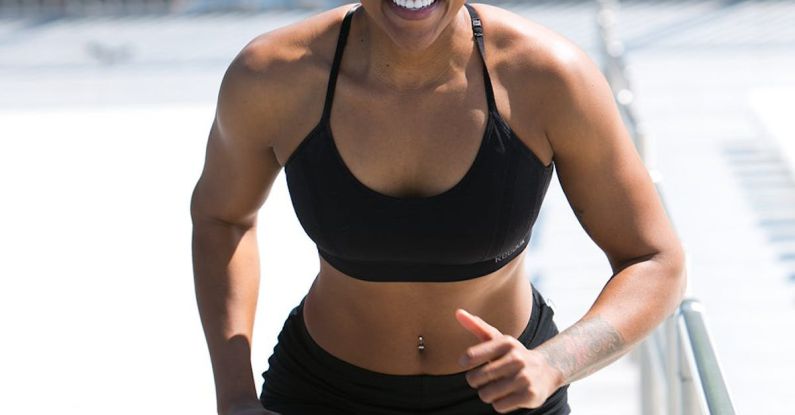
Weight constraints in mobile robotics present a significant challenge in the field of robotics engineering. As the demand for more advanced and efficient robotic systems continues to grow, finding solutions to overcome weight limitations becomes crucial. In this article, we will explore the implications of weight constraints in mobile robotics and discuss potential solutions to address this issue.
Understanding Weight Constraints in Mobile Robotics
Mobile robotics involves the design and development of robots capable of moving in various environments to perform specific tasks. These robots are often equipped with sensors, processors, actuators, and other components essential for their operation. However, the weight of these components can be a limiting factor in the performance and mobility of the robot.
Weight constraints in mobile robotics can impact several aspects of a robot’s functionality. Excessive weight can lead to increased energy consumption, reduced speed and agility, limited payload capacity, and decreased overall performance. Moreover, weight constraints can also affect the structural integrity of the robot, leading to potential mechanical issues and shorter lifespan.
Solutions to Address Weight Constraints
1. Lightweight Materials and Components
One of the primary solutions to overcome weight constraints in mobile robotics is the use of lightweight materials and components. By replacing heavy materials with lighter alternatives such as carbon fiber, aluminum, or composites, engineers can significantly reduce the overall weight of the robot without compromising its structural integrity. Additionally, using lightweight components such as motors, batteries, and sensors can further contribute to weight reduction.
2. Miniaturization and Integration
Another approach to address weight constraints is through miniaturization and integration of components. By shrinking the size of individual components and integrating multiple functions into a single unit, engineers can reduce the overall weight of the robot while maintaining its functionality. For example, combining sensors with processing units or integrating actuators into the robot’s structure can help save space and weight.
3. Optimization of Design
Optimizing the design of the robot is essential to minimize weight while maximizing performance. Engineers can use advanced computer-aided design (CAD) tools to analyze the structural integrity of the robot and identify areas where weight can be reduced without compromising strength. By optimizing the placement of components, streamlining the robot’s body shape, and reducing unnecessary features, engineers can create a more lightweight and efficient robot.
4. Energy-Efficient Systems
Incorporating energy-efficient systems into the robot can also help reduce weight constraints. By using lightweight batteries with high energy density, implementing efficient motor systems, and optimizing power management algorithms, engineers can enhance the robot’s energy efficiency while keeping its weight to a minimum. Additionally, using renewable energy sources such as solar panels can further reduce the reliance on heavy batteries.
5. Modular Design
Implementing a modular design approach can also aid in overcoming weight constraints in mobile robotics. By dividing the robot into smaller modules that can be easily assembled and disassembled, engineers can facilitate maintenance, upgrades, and repairs without the need to replace the entire robot. Moreover, a modular design allows for flexibility in customizing the robot’s configuration based on specific tasks and environments, reducing the overall weight of unnecessary components.
Innovations in Mobile Robotics
The field of mobile robotics continues to evolve with innovations that push the boundaries of what is possible. From autonomous drones and rovers to agile humanoid robots, researchers and engineers are constantly exploring new solutions to enhance the capabilities of robotic systems. By addressing weight constraints through advancements in materials, design, and energy efficiency, the future of mobile robotics looks promising.
In conclusion, weight constraints in mobile robotics present a complex challenge that requires innovative solutions to overcome. By leveraging lightweight materials, miniaturization, design optimization, energy-efficient systems, and modular design, engineers can develop mobile robots that are not only lightweight but also efficient and high-performing. As the field of robotics continues to advance, finding creative solutions to address weight limitations will be crucial in shaping the future of mobile robotics.