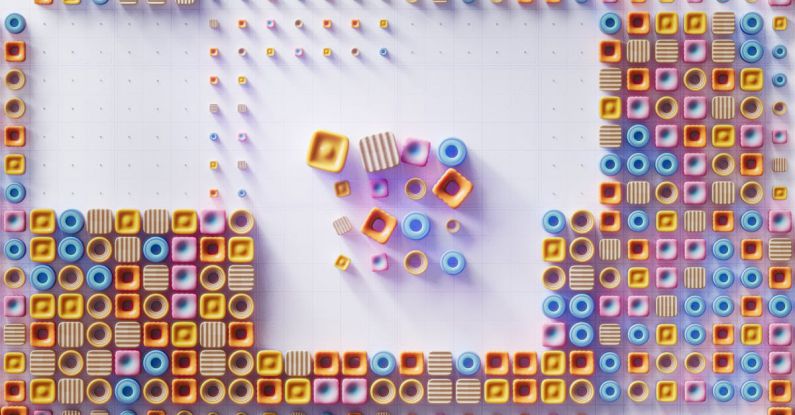
Ensuring the Reliability of Critical Robotic Applications: Can Redundancy Systems Prevent Failures?
The integration of robotic systems in various critical applications, such as manufacturing, healthcare, and space exploration, has significantly increased in recent years. While these robots offer numerous benefits, including increased efficiency and accuracy, they also come with the potential for system failures that could have catastrophic consequences. To mitigate the risks associated with such failures, engineers have turned to redundancy systems as a possible solution. But can redundancy systems truly prevent failures in critical robotic applications?
Understanding the Role of Redundancy Systems
In the realm of robotics, redundancy systems refer to the incorporation of duplicated components or subsystems within a robotic system. These redundancies serve as backup mechanisms that can take over in the event of a primary system failure, thereby reducing the likelihood of a complete system breakdown. By providing multiple pathways for critical functions to be performed, redundancy systems aim to enhance the overall reliability and fault tolerance of robotic applications.
Enhancing Fault Tolerance in Critical Environments
One of the primary advantages of redundancy systems in critical robotic applications is their ability to enhance fault tolerance. In high-stakes environments where system failures can lead to significant financial losses or pose a threat to human safety, having backup systems in place can be a game-changer. Redundancy systems allow robots to continue operating even when certain components malfunction, ensuring that critical tasks are completed without disruption.
Improving System Reliability and Performance
In addition to bolstering fault tolerance, redundancy systems also play a crucial role in improving the overall reliability and performance of robotic applications. By distributing the workload across redundant components, these systems can help prevent overloading of individual parts, thereby extending the lifespan of the robot and reducing the likelihood of unexpected failures. This improved reliability translates to enhanced performance, as robots equipped with redundancy systems can operate more efficiently and consistently under various conditions.
Addressing Safety Concerns in Human-Robot Interaction
As robots become more integrated into human-centric environments, such as healthcare and collaborative manufacturing settings, ensuring the safety of human operators becomes paramount. Redundancy systems can play a vital role in addressing safety concerns related to human-robot interaction by providing fail-safe mechanisms that can quickly detect and respond to potential hazards. In scenarios where human lives are at stake, the presence of redundancy systems can offer an added layer of protection and peace of mind.
Challenges and Considerations in Implementing Redundancy Systems
While redundancy systems hold great promise in enhancing the reliability of critical robotic applications, their implementation is not without challenges. One of the primary considerations is the added cost and complexity associated with incorporating redundant components into robotic systems. Engineers must weigh the benefits of redundancy against the increased upfront investment and potential maintenance requirements to determine the most cost-effective solution for a given application.
Furthermore, designing effective redundancy systems requires a deep understanding of the specific failure modes and operational requirements of the robotic application. Identifying critical components that warrant redundancy, determining the appropriate level of redundancy needed, and implementing seamless failover mechanisms are all crucial steps in ensuring the success of redundancy systems in preventing failures.
Conclusion: Redundancy Systems as a Pillar of Robotic Reliability
In conclusion, the integration of redundancy systems in critical robotic applications holds immense potential for preventing failures and enhancing system reliability. By providing backup mechanisms that can step in when primary systems falter, redundancy systems offer a robust solution for mitigating risks in high-stakes environments. While challenges exist in implementing and maintaining redundancy systems, the benefits they bring in terms of fault tolerance, safety, and performance far outweigh the associated costs. As the field of robotics continues to advance, redundancy systems are poised to play a crucial role in ensuring the seamless operation of critical robotic applications.