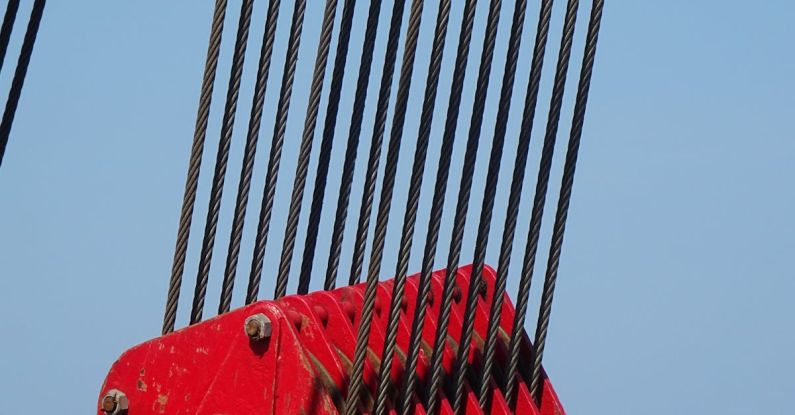
In today’s rapidly advancing technological landscape, robots are increasingly being utilized in a wide range of industries and applications. From manufacturing to agriculture, robots play a crucial role in streamlining processes and increasing efficiency. However, one of the biggest challenges faced by robotics engineers is ensuring the durability of robots in harsh environments. Harsh environments such as extreme temperatures, high humidity, dust, and vibrations can significantly impact the performance and longevity of robots. In this article, we will explore some key strategies to improve the durability of robots in such challenging conditions.
Understanding the Environmental Challenges
Before delving into specific strategies to improve the durability of robots in harsh environments, it is essential to first understand the environmental challenges that robots may encounter. Extreme temperatures, whether hot or cold, can affect the performance of electronic components and motors. High humidity can lead to corrosion and short circuits. Dust and debris can clog sensors and moving parts, while vibrations can cause mechanical wear and tear. By gaining a comprehensive understanding of these challenges, engineers can develop targeted solutions to mitigate their impact on robot durability.
Selecting Robust Materials and Components
One of the most fundamental ways to enhance the durability of robots in harsh environments is to carefully select robust materials and components during the design phase. Choosing materials that are resistant to temperature fluctuations, moisture, and corrosion can significantly increase the lifespan of the robot. Additionally, opting for high-quality components that are rated for the specific environmental conditions in which the robot will operate is crucial. For example, using sealed motors and connectors can help prevent dust and moisture from infiltrating the robot’s internal components.
Implementing Effective Sealing and Enclosures
Sealing and enclosing the critical components of a robot is essential for protecting them from environmental hazards. Rubber gaskets, O-rings, and seals can be used to create a barrier against dust, water, and other contaminants. Enclosures made of durable materials such as aluminum or stainless steel can provide an added layer of protection. It is important to ensure that the seals and enclosures are properly designed and installed to prevent any gaps or weak points that could compromise the robot’s resilience to harsh conditions.
Enhancing Thermal Management
Maintaining optimal operating temperatures is crucial for the longevity of a robot, especially in extreme environments. Implementing effective thermal management solutions such as heat sinks, fans, and thermal insulation can help regulate the temperature of critical components. In hot environments, cooling systems can prevent overheating, while in cold environments, insulation can prevent components from becoming too cold. By carefully managing thermal conditions, engineers can prevent premature component failure and ensure consistent performance.
Integrating Environmental Sensors and Monitoring Systems
To proactively address environmental challenges, integrating environmental sensors and monitoring systems into the robot’s design can be highly beneficial. These sensors can provide real-time data on temperature, humidity, dust levels, and other environmental parameters, allowing the robot to adjust its operations accordingly. By continuously monitoring the environmental conditions, the robot can take preventive measures to avoid potential damage and optimize its performance in harsh environments.
Adopting Robust Mechanical Designs
In addition to selecting durable materials and components, adopting robust mechanical designs is essential for improving the durability of robots in harsh environments. Designing mechanisms with proper sealing, shock absorption, and vibration damping features can help reduce wear and tear on moving parts. Reinforcing structural components to withstand mechanical stresses and impacts can also enhance the overall ruggedness of the robot. By prioritizing robust mechanical design principles, engineers can ensure that the robot can withstand the rigors of harsh operating conditions.
Conclusion:
Ensuring the durability of robots in harsh environments is a multifaceted challenge that requires a combination of strategic design choices and proactive measures. By understanding the environmental challenges, selecting robust materials and components, implementing effective sealing and enclosures, enhancing thermal management, integrating environmental sensors, and adopting robust mechanical designs, engineers can significantly improve the resilience of robots operating in extreme conditions. As technology continues to evolve, the ability to design robots that can thrive in harsh environments will be essential for unlocking new possibilities in various industries.